This article has been:Browse 2139Times Download 2960Times |
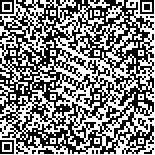 scan it! |
|
DOI:10.13522/j.cnki.ggps.20190018 |
|
Optimal Design of Vortex Pump Using Approximate Model and the Non-dominated Sorting Genetic Algorithm |
YE Daoxing, LI Hao, MA Qiuyan,HAN Qibiao,SUN Xiulu
|
1.Farmland Irrigation Research Institute, CAAS/Key Laboratory of Water-saving Agriculture of Henan Province, Xinxiang 450002, China; 2.Key Laboratory of Fluid and Power Machinery, Ministry of Education, Xihua University,Chengdu 610039, China; 3.Henan Institute of Science and Technology, Xinxiang 453002, China
|
Abstract: |
【Objective】The cavity width L, blade width b2 and the number of blades Z are the most important geometric parameters affecting the performance of vortex pump. This paper aims to present a method to optimize the vortex pump.【Method】 The study was based on approximate model and the non-dominated sorting genetic algorithm II (NSGA-II), in which the pump cavity length, blade width and the number of blades were calculated using the central composite design of DoE (design of experiment). The performance of the designed pump was examined using CFD, and the effect of L, b2 and Z on vortex pump efficiency and shear stress on the blade wall was calculated using the Kriging model. The NSGA-II was used to optimize the geometric parameters. 【Result】The optimal parameters calculated from the methods were L=25 mm, Z=8, b2=26.45 mm.【Conclusion】We proved that CFD and NSGA-II can be used in a combination to calculate the optimal parameters of the vortex pump, and they can significantly improve efficiency of the pump and reduce the shear stress on the blade. Our results revealed that the optimization can reduce the width of the non-blade cavity by 16.67%, and increase the number of blades of the impeller and the outlet width of the blade by 1 and 25.95% respectively. At the design flow rate, the optimal design increased pump efficiency by 1.06% and reduced the average shear stress on the blade from 274.37 Pa to 204.57 Pa. The optimal design made the shear stress on the blade more uniform, in addition to reducing the shear stress on the outlet of the blade. |
Key words: vortex pump, performance optimization, blade surface shear stress, efficiency; NSGA-II algorithm |
|
|